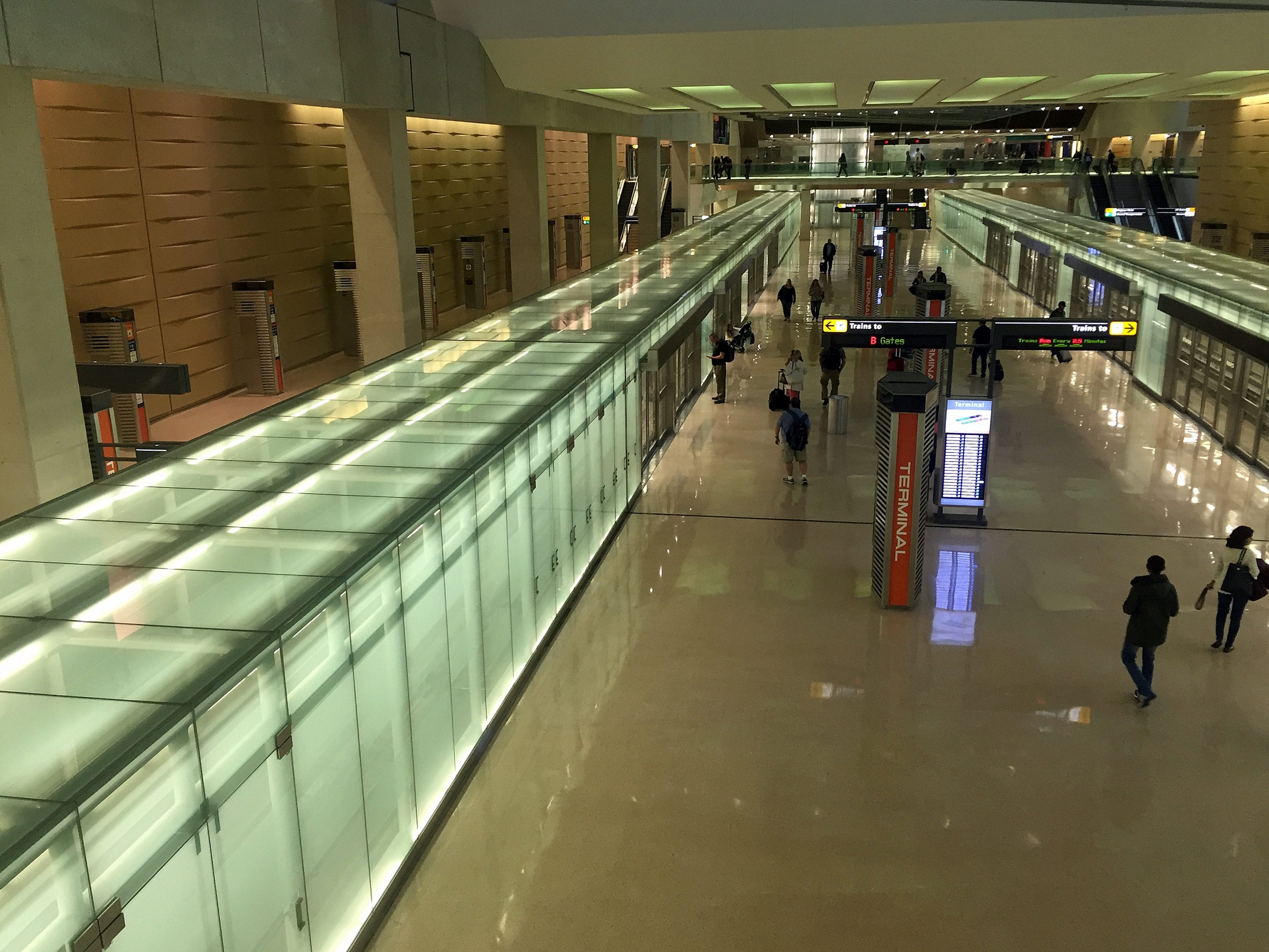
EpiMax supplies both protective sealers and densifiers for polished concrete work.
What are some of the selection influencing factors?
Firstly, a sealer applicator has many choices. Most concrete surfaces can be appropriately prepared and then sealed to meet the end user’s specifications.
What does appropriately prepared mean?
Apart from being of adequate age, quality and strength and being free of osmosis, the slab should be prepared in accordance with the ICRI Surface Preparation standards.
Then a sealer can be installed to look as specified and perform as described in the manufacturer’s technical specifications.
If a “polished concrete look” with a clear topical sealer is required, it is generally accepted that the grind level should be no coarser than that achieved with 100-grit resin bond.
However, true polished concrete, is a manipulation of an existing surface. This manipulation involves the combined action of planetary diamond grinders and suitable silicate based densifiers which work to expose and then harden the top surface of the slab. Depending on the successive range of diamond grits selected, different degrees of aggregate exposure and different levels of sheen, from matt to a glassy mirror-like finish can be achieved
Ideally, the concrete should be formulated, mixed and poured with polishing in mind, to present the selected aggregate colours and sizes.
So what, exactly, are the guidelines for specifying a topical coating instead of densified polished concrete?
One answer is architectural appeal. It can be modern and elegant.
Polished concrete has an appeal of its own. It is incorporated into high end residential and commercial settings.
Professionally installed, it is also easy to clean and durable.
Another answer is function.
Aesthetics aside, if the project requires food safety certification, medical / sanitation certification and visual and tactile pedestrian / vehicle traffic anti-slip safety requirements, polished concrete can be problematic.
Chemical and abrasion resistance is not generally achieved unless a topical sealer is applied.
Adequate stain resistance to hydraulic fluids is also a consideration.
True densified polished concrete is very much dependent on the quality and nature of the starting existing slab. Few polishing contractors can control a new polish job from kick-off to an extent where they can dictate the mix design, delivery, pour, screeding, finishing, curing and floor protection before polishing. Any one of those items handled incorrectly can — and probably will — affect the aesthetic outcome of the project.
If is an existing slab, progress can be compromised by pre-existing utility penetrations and drains that have been patched as well as cracks, flooring adhesives, chemical / oil stains, and sometimes just poor quality concrete.
It is always the best situation for the slab to use a mix design and then be poured with the polishing requirement in mind, in the first place.
When a true polished concrete slab can be designed and managed from the ground up, maintenance is minimal.
CATEGORIES
Knowledge value at your fingertips
SIGNUP NOW
Signup to the Knowledge Centre.